What is the Mainstream Battery Charger Production Process?
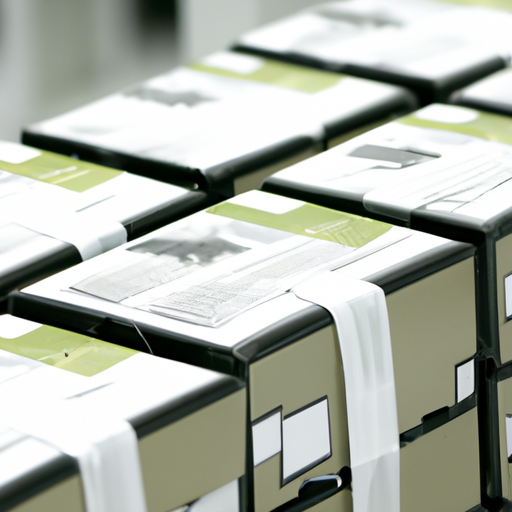
I. Introduction
In our increasingly technology-driven world, battery chargers play a crucial role in ensuring that our devices remain powered and functional. From smartphones to electric vehicles, the demand for reliable and efficient battery chargers has surged. This blog post will explore the mainstream production process of battery chargers, shedding light on the various stages involved, from design to post-production support.
II. Design and Development
A. Conceptualization
The production of a battery charger begins with conceptualization, which involves extensive market research to understand consumer needs and preferences. Manufacturers analyze trends, gather feedback, and identify gaps in the market to create a product that meets the demands of users. This phase often results in initial design sketches and specifications that outline the charger’s features, size, and functionality.
B. Prototyping
Once the initial design is established, the next step is prototyping. This involves creating functional prototypes that allow designers and engineers to test the charger’s performance and usability. Prototyping is an iterative process; feedback from testing leads to modifications and improvements. This stage is critical for identifying potential issues before mass production begins.
C. Final Design Approval
After several rounds of testing and iteration, the final design must receive approval. This includes ensuring compliance with industry standards, such as safety regulations and performance benchmarks. Additionally, the design must be optimized for manufacturability, meaning it should be easy to produce at scale without compromising quality.
III. Sourcing Materials
A. Components of a Battery Charger
The next phase in the production process is sourcing materials. A battery charger consists of several key components, including power supply units, circuit boards, connectors, and cables. Each of these components must be carefully selected to ensure compatibility and performance.
B. Supplier Selection
Choosing the right suppliers is crucial for maintaining quality and reliability. Manufacturers establish criteria for selecting suppliers, which may include factors such as cost, quality assurance measures, and delivery timelines. Building strong relationships with suppliers can lead to better pricing and more reliable supply chains.
C. Procurement Process
Once suppliers are selected, the procurement process begins. This often involves bulk purchasing to reduce costs and ensure a steady supply of materials. Effective inventory management is essential during this stage to prevent shortages or overstocking, which can disrupt production schedules.
IV. Manufacturing Process
A. Assembly Line Setup
With materials in hand, the manufacturing process can commence. This begins with setting up the assembly line, which involves designing the layout and workflow to maximize efficiency. The right equipment and tools are essential for ensuring that each stage of assembly is performed accurately and quickly.
B. Component Assembly
The assembly process involves several steps, including soldering circuit boards, integrating power supply units, and installing connectors and enclosures. Each component must be assembled with precision to ensure the final product functions correctly. Skilled technicians often oversee this process to maintain high standards of quality.
C. Quality Control During Assembly
Quality control is a critical aspect of the manufacturing process. In-process inspections are conducted to identify any defects or issues early on. Additionally, functionality testing is performed to ensure that each charger meets performance specifications before moving on to the next stage.
V. Testing and Quality Assurance
A. Final Product Testing
Once the chargers are assembled, they undergo rigorous final product testing. This includes electrical safety tests to ensure that the chargers are safe for consumer use. Performance evaluations are also conducted to verify that the chargers meet the required specifications for charging speed and efficiency.
B. Compliance with Regulations
Compliance with international standards is essential for battery chargers. Manufacturers must ensure that their products meet regulations such as CE (Conformité Européenne) and UL (Underwriters Laboratories) certifications. Environmental considerations, such as adherence to RoHS (Restriction of Hazardous Substances), are also critical in today’s eco-conscious market.
C. Documentation and Certification
After testing and compliance checks, manufacturers create technical documentation that outlines the charger’s specifications, safety features, and usage instructions. This documentation is essential for certification processes, which may involve third-party testing and validation to ensure that the product meets all necessary standards.
VI. Packaging and Distribution
A. Packaging Design
Once the chargers are certified, the next step is packaging. Packaging design is not only about aesthetics; it also involves branding and marketing considerations. The packaging must protect the chargers during shipping while also appealing to consumers on retail shelves.
B. Distribution Channels
With the product packaged, manufacturers must determine their distribution channels. This may involve forming partnerships with retail outlets or utilizing online sales platforms. A well-planned distribution strategy ensures that the chargers reach consumers efficiently and effectively.
C. Logistics and Supply Chain Management
Logistics and supply chain management play a vital role in the distribution process. Manufacturers must manage inventory levels to meet demand while minimizing excess stock. Efficient shipping and handling processes are also essential to ensure that products arrive at their destinations on time and in good condition.
VII. Post-Production Support
A. Customer Service and Warranty
After the chargers are sold, manufacturers must provide post-production support. This includes customer service to handle inquiries and address any issues that may arise. Warranty policies are also established to protect consumers and build trust in the brand.
B. Feedback and Continuous Improvement
Gathering customer feedback is crucial for continuous improvement. Manufacturers often implement systems to collect feedback on product performance and user experience. This information can lead to design changes and enhancements in future production runs, ensuring that the products remain competitive in the market.
VIII. Conclusion
In conclusion, the production process of battery chargers is a complex and multifaceted endeavor that requires careful planning, execution, and ongoing support. From the initial design and development stages to sourcing materials, manufacturing, testing, and post-production support, each step is critical to delivering a high-quality product that meets consumer needs.
As technology continues to evolve, the significance of quality and innovation in battery charger production cannot be overstated. Future trends may include advancements in fast-charging technology, wireless charging solutions, and eco-friendly materials, all of which will shape the next generation of battery chargers. By understanding the production process, consumers can appreciate the effort and expertise that goes into creating the chargers that power their devices.
What is the Mainstream Battery Charger Production Process?
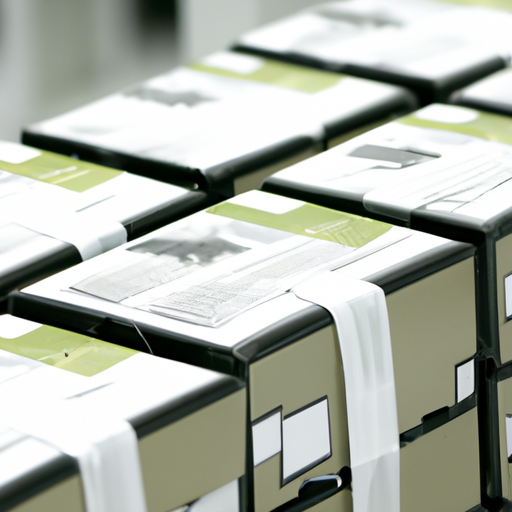
I. Introduction
In our increasingly technology-driven world, battery chargers play a crucial role in ensuring that our devices remain powered and functional. From smartphones to electric vehicles, the demand for reliable and efficient battery chargers has surged. This blog post will explore the mainstream production process of battery chargers, shedding light on the various stages involved, from design to post-production support.
II. Design and Development
A. Conceptualization
The production of a battery charger begins with conceptualization, which involves extensive market research to understand consumer needs and preferences. Manufacturers analyze trends, gather feedback, and identify gaps in the market to create a product that meets the demands of users. This phase often results in initial design sketches and specifications that outline the charger’s features, size, and functionality.
B. Prototyping
Once the initial design is established, the next step is prototyping. This involves creating functional prototypes that allow designers and engineers to test the charger’s performance and usability. Prototyping is an iterative process; feedback from testing leads to modifications and improvements. This stage is critical for identifying potential issues before mass production begins.
C. Final Design Approval
After several rounds of testing and iteration, the final design must receive approval. This includes ensuring compliance with industry standards, such as safety regulations and performance benchmarks. Additionally, the design must be optimized for manufacturability, meaning it should be easy to produce at scale without compromising quality.
III. Sourcing Materials
A. Components of a Battery Charger
The next phase in the production process is sourcing materials. A battery charger consists of several key components, including power supply units, circuit boards, connectors, and cables. Each of these components must be carefully selected to ensure compatibility and performance.
B. Supplier Selection
Choosing the right suppliers is crucial for maintaining quality and reliability. Manufacturers establish criteria for selecting suppliers, which may include factors such as cost, quality assurance measures, and delivery timelines. Building strong relationships with suppliers can lead to better pricing and more reliable supply chains.
C. Procurement Process
Once suppliers are selected, the procurement process begins. This often involves bulk purchasing to reduce costs and ensure a steady supply of materials. Effective inventory management is essential during this stage to prevent shortages or overstocking, which can disrupt production schedules.
IV. Manufacturing Process
A. Assembly Line Setup
With materials in hand, the manufacturing process can commence. This begins with setting up the assembly line, which involves designing the layout and workflow to maximize efficiency. The right equipment and tools are essential for ensuring that each stage of assembly is performed accurately and quickly.
B. Component Assembly
The assembly process involves several steps, including soldering circuit boards, integrating power supply units, and installing connectors and enclosures. Each component must be assembled with precision to ensure the final product functions correctly. Skilled technicians often oversee this process to maintain high standards of quality.
C. Quality Control During Assembly
Quality control is a critical aspect of the manufacturing process. In-process inspections are conducted to identify any defects or issues early on. Additionally, functionality testing is performed to ensure that each charger meets performance specifications before moving on to the next stage.
V. Testing and Quality Assurance
A. Final Product Testing
Once the chargers are assembled, they undergo rigorous final product testing. This includes electrical safety tests to ensure that the chargers are safe for consumer use. Performance evaluations are also conducted to verify that the chargers meet the required specifications for charging speed and efficiency.
B. Compliance with Regulations
Compliance with international standards is essential for battery chargers. Manufacturers must ensure that their products meet regulations such as CE (Conformité Européenne) and UL (Underwriters Laboratories) certifications. Environmental considerations, such as adherence to RoHS (Restriction of Hazardous Substances), are also critical in today’s eco-conscious market.
C. Documentation and Certification
After testing and compliance checks, manufacturers create technical documentation that outlines the charger’s specifications, safety features, and usage instructions. This documentation is essential for certification processes, which may involve third-party testing and validation to ensure that the product meets all necessary standards.
VI. Packaging and Distribution
A. Packaging Design
Once the chargers are certified, the next step is packaging. Packaging design is not only about aesthetics; it also involves branding and marketing considerations. The packaging must protect the chargers during shipping while also appealing to consumers on retail shelves.
B. Distribution Channels
With the product packaged, manufacturers must determine their distribution channels. This may involve forming partnerships with retail outlets or utilizing online sales platforms. A well-planned distribution strategy ensures that the chargers reach consumers efficiently and effectively.
C. Logistics and Supply Chain Management
Logistics and supply chain management play a vital role in the distribution process. Manufacturers must manage inventory levels to meet demand while minimizing excess stock. Efficient shipping and handling processes are also essential to ensure that products arrive at their destinations on time and in good condition.
VII. Post-Production Support
A. Customer Service and Warranty
After the chargers are sold, manufacturers must provide post-production support. This includes customer service to handle inquiries and address any issues that may arise. Warranty policies are also established to protect consumers and build trust in the brand.
B. Feedback and Continuous Improvement
Gathering customer feedback is crucial for continuous improvement. Manufacturers often implement systems to collect feedback on product performance and user experience. This information can lead to design changes and enhancements in future production runs, ensuring that the products remain competitive in the market.
VIII. Conclusion
In conclusion, the production process of battery chargers is a complex and multifaceted endeavor that requires careful planning, execution, and ongoing support. From the initial design and development stages to sourcing materials, manufacturing, testing, and post-production support, each step is critical to delivering a high-quality product that meets consumer needs.
As technology continues to evolve, the significance of quality and innovation in battery charger production cannot be overstated. Future trends may include advancements in fast-charging technology, wireless charging solutions, and eco-friendly materials, all of which will shape the next generation of battery chargers. By understanding the production process, consumers can appreciate the effort and expertise that goes into creating the chargers that power their devices.