Common Production Processes for Horizontal Battery Holders
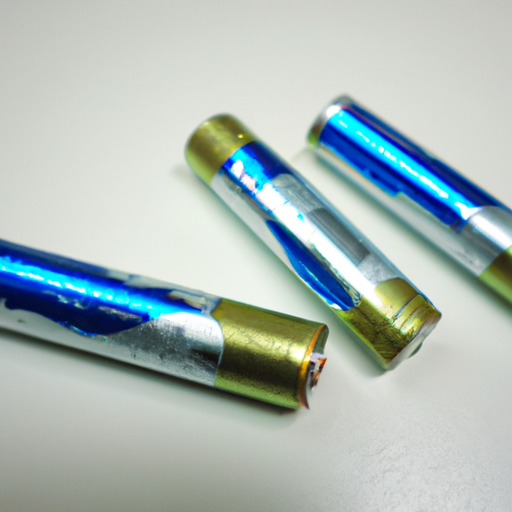
I. Introduction
In the world of electronics, battery holders play a crucial role in ensuring that devices operate efficiently and reliably. Horizontal battery holders, specifically designed to accommodate batteries in a flat orientation, are widely used in various applications, from consumer electronics to industrial equipment. These holders not only secure the batteries but also facilitate easy replacement and maintenance. Understanding the common production processes for horizontal battery holders is essential for manufacturers aiming to produce high-quality components that meet the demands of modern technology.
II. Materials Used in Horizontal Battery Holders
A. Types of Materials
The choice of materials for horizontal battery holders is critical, as it directly impacts the durability, cost, and performance of the final product. The most common materials used include:
1. **Plastic**: Often the material of choice due to its lightweight and cost-effective nature. Plastics like ABS (Acrylonitrile Butadiene Styrene) and polycarbonate are popular for their strength and resistance to impact.
2. **Metal**: Metals such as aluminum and stainless steel are used for their superior strength and electrical conductivity. Metal holders are often preferred in applications where durability and heat dissipation are critical.
3. **Composite Materials**: These materials combine the benefits of plastics and metals, offering enhanced strength and reduced weight. Composites are increasingly being used in high-performance applications.
B. Material Selection Criteria
When selecting materials for horizontal battery holders, manufacturers consider several factors:
1. **Durability**: The material must withstand mechanical stress and environmental conditions without degrading.
2. **Cost-effectiveness**: Balancing quality and cost is essential for competitive pricing in the market.
3. **Electrical Conductivity**: For metal holders, ensuring good electrical conductivity is vital for efficient battery performance.
III. Design and Prototyping
A. Importance of Design in Production
The design phase is crucial in the production of horizontal battery holders. A well-thought-out design ensures that the holder fits the battery securely, allows for easy insertion and removal, and meets the specific requirements of the device it will be used in.
B. Computer-Aided Design (CAD) Software
Modern design processes often utilize CAD software, which allows engineers to create precise 3D models of battery holders. This technology enables quick modifications and optimizations, ensuring that the final design meets all functional and aesthetic requirements.
C. Prototyping Methods
Prototyping is an essential step in the design process, allowing manufacturers to test and refine their designs before mass production. Common prototyping methods include:
1. **3D Printing**: This method allows for rapid prototyping, enabling designers to create physical models quickly and cost-effectively.
2. **CNC Machining**: Computer Numerical Control (CNC) machining provides high precision in creating prototypes from various materials, including metals and plastics.
3. **Injection Molding**: While primarily a production method, injection molding can also be used for prototyping, especially for complex designs that require high accuracy.
IV. Manufacturing Processes
A. Injection Molding
1. Overview of the Process
Injection molding is one of the most common manufacturing processes for producing horizontal battery holders. In this process, molten plastic is injected into a mold, where it cools and solidifies into the desired shape.
2. Advantages and Disadvantages
The advantages of injection molding include high production rates, the ability to create complex shapes, and minimal waste. However, the initial setup costs for molds can be high, making it less economical for small production runs.
B. Stamping and Die-Cutting
1. Description of the Process
Stamping and die-cutting are processes used primarily for metal battery holders. In stamping, a die is used to cut and shape metal sheets into the desired form. This method is efficient for high-volume production.
2. Applications in Battery Holder Production
These processes are particularly useful for creating components that require precise dimensions and high strength, making them ideal for applications in automotive and industrial sectors.
C. Assembly Processes
1. Manual Assembly
In some cases, especially for low-volume production or custom designs, manual assembly is employed. Skilled workers assemble the components by hand, ensuring quality and attention to detail.
2. Automated Assembly Lines
For high-volume production, automated assembly lines are used. These lines utilize robotics and conveyor systems to streamline the assembly process, reducing labor costs and increasing efficiency.
D. Surface Finishing
1. Importance of Surface Treatment
Surface finishing is crucial for enhancing the appearance and performance of battery holders. It can improve corrosion resistance, reduce friction, and enhance electrical conductivity.
2. Common Finishing Techniques
Common surface finishing techniques include:
Painting: Provides aesthetic appeal and protection against environmental factors.
Plating: Electroplating or galvanizing can enhance conductivity and corrosion resistance.
V. Quality Control Measures
A. Importance of Quality Assurance in Production
Quality control is vital in the production of horizontal battery holders to ensure that they meet safety and performance standards. Implementing rigorous quality assurance processes helps prevent defects and ensures customer satisfaction.
B. Testing Methods
Several testing methods are employed to ensure the quality of battery holders:
1. **Dimensional Inspection**: Verifying that the dimensions of the holders meet design specifications.
2. **Functional Testing**: Ensuring that the battery holders perform as intended, including secure battery retention and electrical connectivity.
3. **Environmental Testing**: Assessing the performance of battery holders under various environmental conditions, such as temperature and humidity.
C. Certification Standards
Manufacturers often seek certification to standards such as ISO (International Organization for Standardization) and RoHS (Restriction of Hazardous Substances) to demonstrate compliance with industry regulations and environmental standards.
VI. Environmental Considerations
A. Sustainable Materials and Practices
As environmental concerns grow, manufacturers are increasingly focusing on sustainable materials and practices. This includes using recycled materials and developing eco-friendly production processes.
B. Waste Management in Production
Effective waste management strategies are essential to minimize the environmental impact of production. This includes recycling scrap materials and reducing energy consumption during manufacturing.
C. Recycling of Battery Holders
At the end of their life cycle, battery holders can often be recycled, particularly those made from plastics and metals. Implementing recycling programs can help reduce waste and promote sustainability.
VII. Future Trends in Battery Holder Production
A. Innovations in Materials and Design
The future of battery holder production is likely to see innovations in materials, such as the development of biodegradable plastics and advanced composites that offer improved performance and sustainability.
B. Automation and Industry 4.0
The rise of Industry 4.0 is transforming manufacturing processes, with increased automation and the integration of smart technologies. This trend is expected to enhance efficiency, reduce costs, and improve product quality.
C. Impact of Electric Vehicles and Renewable Energy Storage
The growing demand for electric vehicles and renewable energy storage solutions is driving innovation in battery holder design and production. Manufacturers are adapting to meet the needs of these emerging markets, focusing on high-capacity and lightweight designs.
VIII. Conclusion
In summary, the production processes for horizontal battery holders encompass a range of materials, design techniques, and manufacturing methods. From the initial design phase to quality control and environmental considerations, each step is crucial in ensuring the production of high-quality battery holders. As technology continues to evolve, manufacturers must embrace continuous improvement and innovation to meet the changing demands of the market. The future of horizontal battery holder production looks promising, with advancements in materials, automation, and sustainability paving the way for more efficient and eco-friendly manufacturing practices.
Common Production Processes for Horizontal Battery Holders
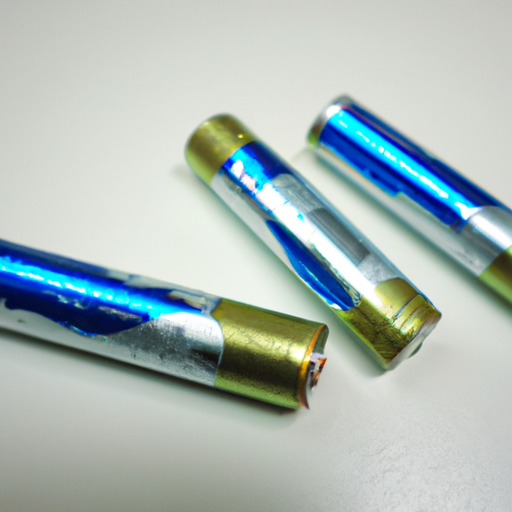
I. Introduction
In the world of electronics, battery holders play a crucial role in ensuring that devices operate efficiently and reliably. Horizontal battery holders, specifically designed to accommodate batteries in a flat orientation, are widely used in various applications, from consumer electronics to industrial equipment. These holders not only secure the batteries but also facilitate easy replacement and maintenance. Understanding the common production processes for horizontal battery holders is essential for manufacturers aiming to produce high-quality components that meet the demands of modern technology.
II. Materials Used in Horizontal Battery Holders
A. Types of Materials
The choice of materials for horizontal battery holders is critical, as it directly impacts the durability, cost, and performance of the final product. The most common materials used include:
1. **Plastic**: Often the material of choice due to its lightweight and cost-effective nature. Plastics like ABS (Acrylonitrile Butadiene Styrene) and polycarbonate are popular for their strength and resistance to impact.
2. **Metal**: Metals such as aluminum and stainless steel are used for their superior strength and electrical conductivity. Metal holders are often preferred in applications where durability and heat dissipation are critical.
3. **Composite Materials**: These materials combine the benefits of plastics and metals, offering enhanced strength and reduced weight. Composites are increasingly being used in high-performance applications.
B. Material Selection Criteria
When selecting materials for horizontal battery holders, manufacturers consider several factors:
1. **Durability**: The material must withstand mechanical stress and environmental conditions without degrading.
2. **Cost-effectiveness**: Balancing quality and cost is essential for competitive pricing in the market.
3. **Electrical Conductivity**: For metal holders, ensuring good electrical conductivity is vital for efficient battery performance.
III. Design and Prototyping
A. Importance of Design in Production
The design phase is crucial in the production of horizontal battery holders. A well-thought-out design ensures that the holder fits the battery securely, allows for easy insertion and removal, and meets the specific requirements of the device it will be used in.
B. Computer-Aided Design (CAD) Software
Modern design processes often utilize CAD software, which allows engineers to create precise 3D models of battery holders. This technology enables quick modifications and optimizations, ensuring that the final design meets all functional and aesthetic requirements.
C. Prototyping Methods
Prototyping is an essential step in the design process, allowing manufacturers to test and refine their designs before mass production. Common prototyping methods include:
1. **3D Printing**: This method allows for rapid prototyping, enabling designers to create physical models quickly and cost-effectively.
2. **CNC Machining**: Computer Numerical Control (CNC) machining provides high precision in creating prototypes from various materials, including metals and plastics.
3. **Injection Molding**: While primarily a production method, injection molding can also be used for prototyping, especially for complex designs that require high accuracy.
IV. Manufacturing Processes
A. Injection Molding
1. Overview of the Process
Injection molding is one of the most common manufacturing processes for producing horizontal battery holders. In this process, molten plastic is injected into a mold, where it cools and solidifies into the desired shape.
2. Advantages and Disadvantages
The advantages of injection molding include high production rates, the ability to create complex shapes, and minimal waste. However, the initial setup costs for molds can be high, making it less economical for small production runs.
B. Stamping and Die-Cutting
1. Description of the Process
Stamping and die-cutting are processes used primarily for metal battery holders. In stamping, a die is used to cut and shape metal sheets into the desired form. This method is efficient for high-volume production.
2. Applications in Battery Holder Production
These processes are particularly useful for creating components that require precise dimensions and high strength, making them ideal for applications in automotive and industrial sectors.
C. Assembly Processes
1. Manual Assembly
In some cases, especially for low-volume production or custom designs, manual assembly is employed. Skilled workers assemble the components by hand, ensuring quality and attention to detail.
2. Automated Assembly Lines
For high-volume production, automated assembly lines are used. These lines utilize robotics and conveyor systems to streamline the assembly process, reducing labor costs and increasing efficiency.
D. Surface Finishing
1. Importance of Surface Treatment
Surface finishing is crucial for enhancing the appearance and performance of battery holders. It can improve corrosion resistance, reduce friction, and enhance electrical conductivity.
2. Common Finishing Techniques
Common surface finishing techniques include:
Painting: Provides aesthetic appeal and protection against environmental factors.
Plating: Electroplating or galvanizing can enhance conductivity and corrosion resistance.
V. Quality Control Measures
A. Importance of Quality Assurance in Production
Quality control is vital in the production of horizontal battery holders to ensure that they meet safety and performance standards. Implementing rigorous quality assurance processes helps prevent defects and ensures customer satisfaction.
B. Testing Methods
Several testing methods are employed to ensure the quality of battery holders:
1. **Dimensional Inspection**: Verifying that the dimensions of the holders meet design specifications.
2. **Functional Testing**: Ensuring that the battery holders perform as intended, including secure battery retention and electrical connectivity.
3. **Environmental Testing**: Assessing the performance of battery holders under various environmental conditions, such as temperature and humidity.
C. Certification Standards
Manufacturers often seek certification to standards such as ISO (International Organization for Standardization) and RoHS (Restriction of Hazardous Substances) to demonstrate compliance with industry regulations and environmental standards.
VI. Environmental Considerations
A. Sustainable Materials and Practices
As environmental concerns grow, manufacturers are increasingly focusing on sustainable materials and practices. This includes using recycled materials and developing eco-friendly production processes.
B. Waste Management in Production
Effective waste management strategies are essential to minimize the environmental impact of production. This includes recycling scrap materials and reducing energy consumption during manufacturing.
C. Recycling of Battery Holders
At the end of their life cycle, battery holders can often be recycled, particularly those made from plastics and metals. Implementing recycling programs can help reduce waste and promote sustainability.
VII. Future Trends in Battery Holder Production
A. Innovations in Materials and Design
The future of battery holder production is likely to see innovations in materials, such as the development of biodegradable plastics and advanced composites that offer improved performance and sustainability.
B. Automation and Industry 4.0
The rise of Industry 4.0 is transforming manufacturing processes, with increased automation and the integration of smart technologies. This trend is expected to enhance efficiency, reduce costs, and improve product quality.
C. Impact of Electric Vehicles and Renewable Energy Storage
The growing demand for electric vehicles and renewable energy storage solutions is driving innovation in battery holder design and production. Manufacturers are adapting to meet the needs of these emerging markets, focusing on high-capacity and lightweight designs.
VIII. Conclusion
In summary, the production processes for horizontal battery holders encompass a range of materials, design techniques, and manufacturing methods. From the initial design phase to quality control and environmental considerations, each step is crucial in ensuring the production of high-quality battery holders. As technology continues to evolve, manufacturers must embrace continuous improvement and innovation to meet the changing demands of the market. The future of horizontal battery holder production looks promising, with advancements in materials, automation, and sustainability paving the way for more efficient and eco-friendly manufacturing practices.