Common Production Processes for Battery Products Shipped by Sea
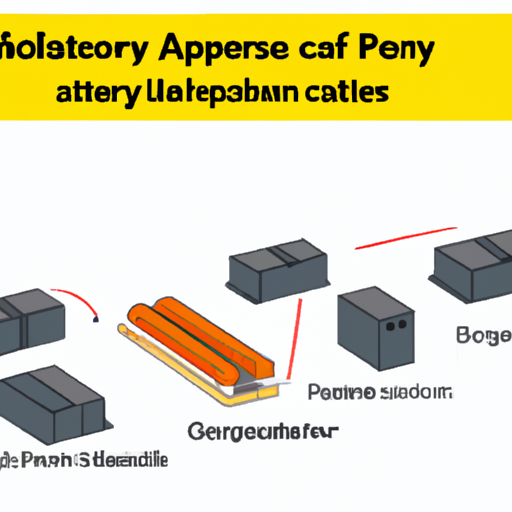
I. Introduction
The battery industry has experienced exponential growth in recent years, driven by the increasing demand for energy storage solutions in various sectors, including electric vehicles, renewable energy, and consumer electronics. As the world shifts towards sustainable energy sources, the importance of efficient and reliable battery production processes cannot be overstated. Shipping battery products by sea is a critical aspect of this industry, as it allows manufacturers to reach global markets while managing costs effectively. This article aims to provide an in-depth overview of the common production processes for battery products that are shipped by sea, highlighting the various stages involved from raw material sourcing to logistics and shipping considerations.
II. Types of Battery Products
Battery technology has evolved significantly, leading to the development of various types of batteries, each with unique characteristics and applications. The most common types include:
A. Lithium-ion Batteries
Lithium-ion batteries are widely used in consumer electronics, electric vehicles, and renewable energy storage systems. They are known for their high energy density, lightweight design, and long cycle life.
B. Lead-acid Batteries
Lead-acid batteries have been in use for over a century and are commonly found in automotive applications and backup power systems. They are cost-effective but have a lower energy density compared to lithium-ion batteries.
C. Nickel-metal Hydride Batteries
Nickel-metal hydride (NiMH) batteries are often used in hybrid vehicles and portable electronics. They offer a good balance between energy density and cost but are gradually being replaced by lithium-ion technology.
D. Other Emerging Battery Technologies
Emerging technologies, such as solid-state batteries and flow batteries, are gaining attention for their potential to improve safety, energy density, and sustainability. These innovations are still in the development phase but could revolutionize the battery industry in the coming years.
III. Overview of Battery Production Processes
The production of battery products involves several key processes, each critical to ensuring the final product's performance and safety.
A. Raw Material Sourcing
1. Mining and Extraction
The first step in battery production is sourcing raw materials, which often involves mining and extraction. For lithium-ion batteries, key materials include lithium, cobalt, nickel, and graphite. These materials are extracted from various sources, including mines and brine deposits.
2. Material Processing
Once extracted, raw materials undergo processing to purify and prepare them for use in battery production. This may involve chemical treatments, milling, and other processes to achieve the desired specifications.
B. Manufacturing Processes
1. Electrode Production
a. Cathode and Anode Materials
The production of electrodes is a crucial step in battery manufacturing. Cathodes are typically made from lithium cobalt oxide or lithium iron phosphate, while anodes are often composed of graphite. The choice of materials affects the battery's performance characteristics.
b. Coating and Drying
After preparing the electrode materials, they are coated onto metal foils (usually aluminum for cathodes and copper for anodes) and dried to remove any solvents. This process is essential for ensuring proper adhesion and performance.
2. Cell Assembly
a. Cell Design and Configuration
Cell assembly involves stacking or winding the coated electrodes with separators to create a cell. The design and configuration depend on the intended application and desired energy density.
b. Electrolyte Filling
Once the cell is assembled, an electrolyte solution is filled into the cell. The electrolyte facilitates the movement of ions between the anode and cathode during charging and discharging.
3. Formation and Aging
a. Initial Charging Cycles
The formation process involves subjecting the battery cells to initial charging cycles, which help to stabilize the materials and improve performance. This step is critical for ensuring the longevity and efficiency of the battery.
b. Quality Control Measures
Quality control measures are implemented throughout the production process to identify and rectify any defects. This includes visual inspections, electrical testing, and performance evaluations.
C. Battery Pack Assembly
1. Module Assembly
After individual cells are produced, they are assembled into modules, which are then combined to form battery packs. This step involves connecting cells in series or parallel configurations to achieve the desired voltage and capacity.
2. Battery Management Systems (BMS)
A Battery Management System (BMS) is integrated into the battery pack to monitor and manage the performance of individual cells. The BMS ensures safe operation, optimizes charging and discharging, and provides data for diagnostics.
3. Packaging for Shipping
Finally, the completed battery packs are packaged for shipping. This involves protective packaging to prevent damage during transport and compliance with hazardous materials regulations.
IV. Quality Control and Testing
A. Importance of Quality Assurance
Quality assurance is paramount in battery production, as defects can lead to safety hazards, reduced performance, and shorter lifespans. Manufacturers implement rigorous quality control measures to ensure that each battery meets industry standards.
B. Testing Procedures
1. Electrical Performance Tests
Electrical performance tests evaluate the battery's capacity, voltage, and discharge rates. These tests help ensure that the battery performs as expected under various conditions.
2. Safety Tests
Safety tests assess the battery's resistance to thermal runaway, short circuits, and other potential hazards. These tests are critical for ensuring the safety of end-users.
3. Environmental Tests
Environmental tests evaluate the battery's performance under extreme temperatures, humidity, and other environmental conditions. This ensures that the battery can operate reliably in various settings.
C. Certification and Compliance Standards
Battery manufacturers must adhere to various certification and compliance standards, such as ISO 9001 for quality management and UN 38.3 for the safe transport of lithium batteries. Compliance with these standards is essential for gaining market access and ensuring safety.
V. Logistics and Shipping Considerations
A. Packaging Requirements for Sea Transport
1. Hazardous Materials Regulations
Shipping batteries by sea involves compliance with hazardous materials regulations, as many battery types contain flammable or toxic substances. Proper labeling and packaging are essential to ensure safe transport.
2. Protective Packaging
Protective packaging is crucial to prevent damage during transit. This may include cushioning materials, moisture barriers, and sturdy outer containers to withstand the rigors of shipping.
B. Shipping Documentation
1. Bill of Lading
A bill of lading is a legal document that outlines the terms of the shipment, including the type and quantity of goods being transported. It serves as a receipt and contract between the shipper and carrier.
2. Safety Data Sheets (SDS)
Safety Data Sheets (SDS) provide essential information about the hazards associated with battery products, including handling, storage, and emergency measures. These documents are crucial for ensuring the safety of personnel involved in shipping and handling.
C. Choosing the Right Shipping Method
1. Container Shipping
Container shipping is the most common method for transporting battery products by sea. Containers provide a secure and efficient way to transport large quantities of goods while minimizing the risk of damage.
2. Specialized Carriers for Hazardous Materials
In some cases, specialized carriers may be required to transport hazardous materials safely. These carriers are equipped to handle the unique challenges associated with shipping battery products.
VI. Environmental and Regulatory Considerations
A. Environmental Impact of Battery Production
Battery production has a significant environmental impact, including resource depletion, pollution, and waste generation. Manufacturers are increasingly focused on minimizing their environmental footprint through sustainable practices.
B. Regulations Governing Battery Shipping
1. International Maritime Organization (IMO) Guidelines
The International Maritime Organization (IMO) has established guidelines for the safe transport of hazardous materials, including batteries. Compliance with these guidelines is essential for ensuring safe shipping practices.
2. Local and National Regulations
In addition to international regulations, manufacturers must also comply with local and national regulations governing battery production and shipping. These regulations may vary by region and can impact shipping logistics.
C. Sustainable Practices in Battery Production and Shipping
Sustainable practices, such as recycling and the use of renewable energy sources, are becoming increasingly important in the battery industry. Manufacturers are exploring ways to reduce waste and improve the sustainability of their production and shipping processes.
VII. Challenges in Battery Production and Shipping
A. Supply Chain Disruptions
The battery industry is susceptible to supply chain disruptions, which can impact the availability of raw materials and increase production costs. Manufacturers must develop strategies to mitigate these risks.
B. Fluctuating Raw Material Prices
Fluctuating prices for raw materials, such as lithium and cobalt, can affect the overall cost of battery production. Manufacturers must navigate these market dynamics to maintain profitability.
C. Safety Concerns During Transport
Safety concerns, such as the risk of thermal runaway or leaks, pose challenges during the transport of battery products. Adhering to safety regulations and implementing best practices is essential for minimizing these risks.
D. Technological Advancements and Their Impact
Technological advancements in battery production and shipping are rapidly evolving. Manufacturers must stay abreast of these changes to remain competitive and ensure the safety and efficiency of their operations.
VIII. Future Trends in Battery Production and Shipping
A. Innovations in Battery Technology
Innovations in battery technology, such as solid-state batteries and advanced recycling methods, are expected to shape the future of the industry. These advancements could lead to safer, more efficient, and environmentally friendly battery products.
B. Evolving Shipping Practices
As the demand for battery products continues to grow, shipping practices will evolve to accommodate new technologies and regulations. This may include the use of automated systems and improved tracking methods.
C. The Role of Automation and AI in Production and Logistics
Automation and artificial intelligence (AI) are increasingly being integrated into battery production and logistics. These technologies can enhance efficiency, reduce costs, and improve safety throughout the supply chain.
IX. Conclusion
In conclusion, understanding the common production processes for battery products shipped by sea is essential for stakeholders in the battery industry. From raw material sourcing to logistics and shipping considerations, each stage plays a critical role in ensuring the safety, performance, and sustainability of battery products. As the industry continues to evolve, staying informed about emerging trends and challenges will be crucial for manufacturers, regulators, and consumers alike. The future of the battery industry holds great promise, with innovations in technology and shipping practices paving the way for a more sustainable and efficient energy landscape.
X. References
- Academic articles on battery technology and production processes
- Industry reports on battery market trends and forecasts
- Regulatory documents from the International Maritime Organization (IMO) and local authorities
- Relevant websites and resources for further reading on battery production and shipping logistics
This comprehensive overview provides a detailed understanding of the production processes for battery products shipped by sea, highlighting the importance of quality control, logistics, and sustainability in the industry.
Common Production Processes for Battery Products Shipped by Sea
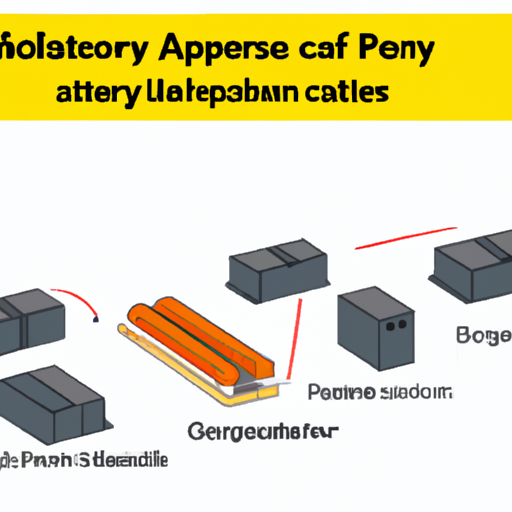
I. Introduction
The battery industry has experienced exponential growth in recent years, driven by the increasing demand for energy storage solutions in various sectors, including electric vehicles, renewable energy, and consumer electronics. As the world shifts towards sustainable energy sources, the importance of efficient and reliable battery production processes cannot be overstated. Shipping battery products by sea is a critical aspect of this industry, as it allows manufacturers to reach global markets while managing costs effectively. This article aims to provide an in-depth overview of the common production processes for battery products that are shipped by sea, highlighting the various stages involved from raw material sourcing to logistics and shipping considerations.
II. Types of Battery Products
Battery technology has evolved significantly, leading to the development of various types of batteries, each with unique characteristics and applications. The most common types include:
A. Lithium-ion Batteries
Lithium-ion batteries are widely used in consumer electronics, electric vehicles, and renewable energy storage systems. They are known for their high energy density, lightweight design, and long cycle life.
B. Lead-acid Batteries
Lead-acid batteries have been in use for over a century and are commonly found in automotive applications and backup power systems. They are cost-effective but have a lower energy density compared to lithium-ion batteries.
C. Nickel-metal Hydride Batteries
Nickel-metal hydride (NiMH) batteries are often used in hybrid vehicles and portable electronics. They offer a good balance between energy density and cost but are gradually being replaced by lithium-ion technology.
D. Other Emerging Battery Technologies
Emerging technologies, such as solid-state batteries and flow batteries, are gaining attention for their potential to improve safety, energy density, and sustainability. These innovations are still in the development phase but could revolutionize the battery industry in the coming years.
III. Overview of Battery Production Processes
The production of battery products involves several key processes, each critical to ensuring the final product's performance and safety.
A. Raw Material Sourcing
1. Mining and Extraction
The first step in battery production is sourcing raw materials, which often involves mining and extraction. For lithium-ion batteries, key materials include lithium, cobalt, nickel, and graphite. These materials are extracted from various sources, including mines and brine deposits.
2. Material Processing
Once extracted, raw materials undergo processing to purify and prepare them for use in battery production. This may involve chemical treatments, milling, and other processes to achieve the desired specifications.
B. Manufacturing Processes
1. Electrode Production
a. Cathode and Anode Materials
The production of electrodes is a crucial step in battery manufacturing. Cathodes are typically made from lithium cobalt oxide or lithium iron phosphate, while anodes are often composed of graphite. The choice of materials affects the battery's performance characteristics.
b. Coating and Drying
After preparing the electrode materials, they are coated onto metal foils (usually aluminum for cathodes and copper for anodes) and dried to remove any solvents. This process is essential for ensuring proper adhesion and performance.
2. Cell Assembly
a. Cell Design and Configuration
Cell assembly involves stacking or winding the coated electrodes with separators to create a cell. The design and configuration depend on the intended application and desired energy density.
b. Electrolyte Filling
Once the cell is assembled, an electrolyte solution is filled into the cell. The electrolyte facilitates the movement of ions between the anode and cathode during charging and discharging.
3. Formation and Aging
a. Initial Charging Cycles
The formation process involves subjecting the battery cells to initial charging cycles, which help to stabilize the materials and improve performance. This step is critical for ensuring the longevity and efficiency of the battery.
b. Quality Control Measures
Quality control measures are implemented throughout the production process to identify and rectify any defects. This includes visual inspections, electrical testing, and performance evaluations.
C. Battery Pack Assembly
1. Module Assembly
After individual cells are produced, they are assembled into modules, which are then combined to form battery packs. This step involves connecting cells in series or parallel configurations to achieve the desired voltage and capacity.
2. Battery Management Systems (BMS)
A Battery Management System (BMS) is integrated into the battery pack to monitor and manage the performance of individual cells. The BMS ensures safe operation, optimizes charging and discharging, and provides data for diagnostics.
3. Packaging for Shipping
Finally, the completed battery packs are packaged for shipping. This involves protective packaging to prevent damage during transport and compliance with hazardous materials regulations.
IV. Quality Control and Testing
A. Importance of Quality Assurance
Quality assurance is paramount in battery production, as defects can lead to safety hazards, reduced performance, and shorter lifespans. Manufacturers implement rigorous quality control measures to ensure that each battery meets industry standards.
B. Testing Procedures
1. Electrical Performance Tests
Electrical performance tests evaluate the battery's capacity, voltage, and discharge rates. These tests help ensure that the battery performs as expected under various conditions.
2. Safety Tests
Safety tests assess the battery's resistance to thermal runaway, short circuits, and other potential hazards. These tests are critical for ensuring the safety of end-users.
3. Environmental Tests
Environmental tests evaluate the battery's performance under extreme temperatures, humidity, and other environmental conditions. This ensures that the battery can operate reliably in various settings.
C. Certification and Compliance Standards
Battery manufacturers must adhere to various certification and compliance standards, such as ISO 9001 for quality management and UN 38.3 for the safe transport of lithium batteries. Compliance with these standards is essential for gaining market access and ensuring safety.
V. Logistics and Shipping Considerations
A. Packaging Requirements for Sea Transport
1. Hazardous Materials Regulations
Shipping batteries by sea involves compliance with hazardous materials regulations, as many battery types contain flammable or toxic substances. Proper labeling and packaging are essential to ensure safe transport.
2. Protective Packaging
Protective packaging is crucial to prevent damage during transit. This may include cushioning materials, moisture barriers, and sturdy outer containers to withstand the rigors of shipping.
B. Shipping Documentation
1. Bill of Lading
A bill of lading is a legal document that outlines the terms of the shipment, including the type and quantity of goods being transported. It serves as a receipt and contract between the shipper and carrier.
2. Safety Data Sheets (SDS)
Safety Data Sheets (SDS) provide essential information about the hazards associated with battery products, including handling, storage, and emergency measures. These documents are crucial for ensuring the safety of personnel involved in shipping and handling.
C. Choosing the Right Shipping Method
1. Container Shipping
Container shipping is the most common method for transporting battery products by sea. Containers provide a secure and efficient way to transport large quantities of goods while minimizing the risk of damage.
2. Specialized Carriers for Hazardous Materials
In some cases, specialized carriers may be required to transport hazardous materials safely. These carriers are equipped to handle the unique challenges associated with shipping battery products.
VI. Environmental and Regulatory Considerations
A. Environmental Impact of Battery Production
Battery production has a significant environmental impact, including resource depletion, pollution, and waste generation. Manufacturers are increasingly focused on minimizing their environmental footprint through sustainable practices.
B. Regulations Governing Battery Shipping
1. International Maritime Organization (IMO) Guidelines
The International Maritime Organization (IMO) has established guidelines for the safe transport of hazardous materials, including batteries. Compliance with these guidelines is essential for ensuring safe shipping practices.
2. Local and National Regulations
In addition to international regulations, manufacturers must also comply with local and national regulations governing battery production and shipping. These regulations may vary by region and can impact shipping logistics.
C. Sustainable Practices in Battery Production and Shipping
Sustainable practices, such as recycling and the use of renewable energy sources, are becoming increasingly important in the battery industry. Manufacturers are exploring ways to reduce waste and improve the sustainability of their production and shipping processes.
VII. Challenges in Battery Production and Shipping
A. Supply Chain Disruptions
The battery industry is susceptible to supply chain disruptions, which can impact the availability of raw materials and increase production costs. Manufacturers must develop strategies to mitigate these risks.
B. Fluctuating Raw Material Prices
Fluctuating prices for raw materials, such as lithium and cobalt, can affect the overall cost of battery production. Manufacturers must navigate these market dynamics to maintain profitability.
C. Safety Concerns During Transport
Safety concerns, such as the risk of thermal runaway or leaks, pose challenges during the transport of battery products. Adhering to safety regulations and implementing best practices is essential for minimizing these risks.
D. Technological Advancements and Their Impact
Technological advancements in battery production and shipping are rapidly evolving. Manufacturers must stay abreast of these changes to remain competitive and ensure the safety and efficiency of their operations.
VIII. Future Trends in Battery Production and Shipping
A. Innovations in Battery Technology
Innovations in battery technology, such as solid-state batteries and advanced recycling methods, are expected to shape the future of the industry. These advancements could lead to safer, more efficient, and environmentally friendly battery products.
B. Evolving Shipping Practices
As the demand for battery products continues to grow, shipping practices will evolve to accommodate new technologies and regulations. This may include the use of automated systems and improved tracking methods.
C. The Role of Automation and AI in Production and Logistics
Automation and artificial intelligence (AI) are increasingly being integrated into battery production and logistics. These technologies can enhance efficiency, reduce costs, and improve safety throughout the supply chain.
IX. Conclusion
In conclusion, understanding the common production processes for battery products shipped by sea is essential for stakeholders in the battery industry. From raw material sourcing to logistics and shipping considerations, each stage plays a critical role in ensuring the safety, performance, and sustainability of battery products. As the industry continues to evolve, staying informed about emerging trends and challenges will be crucial for manufacturers, regulators, and consumers alike. The future of the battery industry holds great promise, with innovations in technology and shipping practices paving the way for a more sustainable and efficient energy landscape.
X. References
- Academic articles on battery technology and production processes
- Industry reports on battery market trends and forecasts
- Regulatory documents from the International Maritime Organization (IMO) and local authorities
- Relevant websites and resources for further reading on battery production and shipping logistics
This comprehensive overview provides a detailed understanding of the production processes for battery products shipped by sea, highlighting the importance of quality control, logistics, and sustainability in the industry.