What are the Manufacturing Processes for the Latest Smart Digital Product Battery Cells?
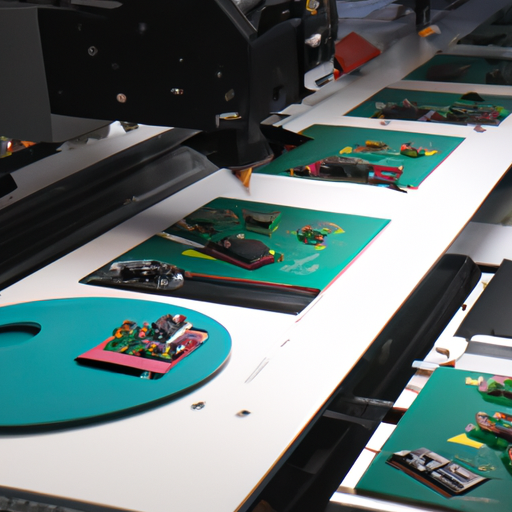
I. Introduction
In an era where smart digital products dominate our daily lives, the importance of advanced battery technology cannot be overstated. From smartphones and laptops to wearables and electric vehicles, these devices rely heavily on efficient, reliable, and long-lasting battery cells. The performance, longevity, and overall user experience of these products are significantly influenced by the quality of their battery cells. This article aims to explore the intricate manufacturing processes behind the latest battery cells used in smart digital products, shedding light on the technologies that power our modern world.
II. Types of Battery Cells Used in Smart Digital Products
A. Lithium-ion (Li-ion) Batteries
Lithium-ion batteries are the most prevalent type of battery used in smart digital products today. Known for their high energy density, lightweight design, and ability to recharge quickly, Li-ion batteries have become the gold standard for portable electronics. They are commonly found in smartphones, laptops, tablets, and electric vehicles, providing the necessary power to keep these devices running efficiently.
B. Solid-state Batteries
Emerging as a promising alternative, solid-state batteries utilize a solid electrolyte instead of a liquid one. This technology offers several advantages, including higher energy density, improved safety, and longer lifespan. While still in the developmental stage, solid-state batteries hold the potential to revolutionize the battery industry, particularly in applications requiring high performance and safety, such as electric vehicles and advanced consumer electronics.
C. Other Battery Technologies
In addition to Li-ion and solid-state batteries, other technologies like lithium polymer (LiPo) and nickel-metal hydride (NiMH) batteries are also used in specific applications. LiPo batteries are favored in devices where weight and form factor are critical, such as drones and wearables. NiMH batteries, while less common in modern smart devices, are still used in some applications due to their reliability and cost-effectiveness.
III. Overview of Battery Cell Manufacturing
The manufacturing of battery cells is a complex process that demands precision and stringent quality control. Each stage of production is crucial to ensure that the final product meets the required performance and safety standards. The key stages in the manufacturing process include material selection, cell design and engineering, and assembly and integration.
IV. Detailed Manufacturing Processes
A. Material Preparation
The first step in battery cell manufacturing is sourcing raw materials, which typically include lithium, cobalt, nickel, and graphite. These materials must undergo purification and processing to remove impurities that could affect battery performance. The quality of the raw materials directly impacts the efficiency and safety of the final battery cells.
B. Electrode Production
Electrode production is a critical phase in battery manufacturing. It involves several steps:
1. **Coating Processes**: A slurry containing active materials, solvents, and binders is coated onto a current collector (usually aluminum for the positive electrode and copper for the negative electrode). This process is crucial for ensuring uniformity and adherence of the active materials.
2. **Drying and Calendaring**: After coating, the electrodes are dried to remove solvents and then passed through rollers (calendaring) to achieve the desired thickness and density.
3. **Cutting and Stacking**: The dried electrodes are cut into specific shapes and sizes, then stacked with separators to form the cell structure.
C. Electrolyte Preparation
The electrolyte is a vital component of battery cells, facilitating the movement of ions between the electrodes. The composition and formulation of electrolytes are carefully designed to optimize performance and safety. Quality checks are performed to ensure that the electrolyte meets the required specifications, including viscosity and conductivity.
D. Cell Assembly
The assembly process involves several steps:
1. **Layering Electrodes and Separators**: The prepared electrodes and separators are layered together in a specific configuration to form the cell.
2. **Filling with Electrolyte**: The assembled cell is filled with the prepared electrolyte, ensuring that all components are adequately saturated.
3. **Sealing and Packaging**: Finally, the cell is sealed to prevent leakage and packaged for distribution. This step is crucial for maintaining the integrity and safety of the battery.
E. Formation and Testing
Once assembled, the battery cells undergo a formation process, which involves initial charging and cycling to activate the materials. This step is essential for ensuring that the battery cells perform as expected. Following formation, rigorous performance testing and quality assurance checks are conducted, including safety testing for thermal, mechanical, and electrical stability.
V. Innovations in Battery Manufacturing
The battery manufacturing landscape is continuously evolving, driven by technological advancements and the need for more efficient production methods. Some notable innovations include:
A. Automation and Robotics
The integration of automation and robotics in battery production has significantly improved efficiency and precision. Automated systems can handle repetitive tasks, reducing the risk of human error and increasing production speed.
B. Advanced Materials and Nanotechnology
Research into advanced materials and nanotechnology is paving the way for the development of next-generation batteries. These innovations aim to enhance energy density, reduce charging times, and improve overall battery performance.
C. Sustainable Manufacturing Practices
As environmental concerns grow, the battery industry is increasingly focusing on sustainable manufacturing practices. This includes recycling and reusing materials, as well as implementing processes that reduce the carbon footprint of production. Companies are exploring ways to minimize waste and energy consumption throughout the manufacturing process.
VI. Challenges in Battery Cell Manufacturing
Despite the advancements in battery technology, several challenges persist in the manufacturing sector:
A. Supply Chain Issues and Material Shortages
The demand for battery materials, particularly lithium and cobalt, has surged, leading to supply chain challenges and material shortages. This can impact production timelines and costs.
B. Environmental Concerns and Regulations
The environmental impact of battery production and disposal is a growing concern. Manufacturers must navigate regulations and implement practices that minimize harm to the environment.
C. Balancing Performance with Cost-Effectiveness
As battery technology advances, manufacturers face the challenge of balancing performance improvements with cost-effectiveness. Developing high-performance batteries that are also affordable for consumers is a critical consideration.
VII. Future Trends in Battery Technology and Manufacturing
The future of battery technology and manufacturing is promising, with several trends on the horizon:
A. Research and Development in Next-Generation Batteries
Ongoing research is focused on developing next-generation batteries, such as lithium-sulfur and lithium-air batteries, which could offer significantly higher energy densities and longer lifespans.
B. The Role of Artificial Intelligence and Machine Learning
Artificial intelligence (AI) and machine learning are increasingly being integrated into battery manufacturing processes. These technologies can optimize production, predict maintenance needs, and enhance quality control.
C. Predictions for the Future of Battery Cells in Smart Digital Products
As smart digital products continue to evolve, the demand for advanced battery cells will only increase. Future trends may include batteries with faster charging capabilities, longer lifespans, and improved safety features, all of which will enhance the user experience.
VIII. Conclusion
The manufacturing processes behind advanced battery cells are complex and multifaceted, playing a crucial role in the performance and longevity of smart digital products. Innovations in battery technology and manufacturing practices are paving the way for a more efficient and sustainable future. As the landscape of battery technology continues to evolve, consumers and manufacturers alike will benefit from the advancements that enhance the functionality and usability of smart devices.
IX. References
1. N. N. (2022). "Advancements in Lithium-Ion Battery Technology." Journal of Power Sources.
2. M. M. (2023). "The Future of Solid-State Batteries." Energy Storage Materials.
3. R. R. (2021). "Sustainable Practices in Battery Manufacturing." Journal of Cleaner Production.
4. T. T. (2023). "AI in Battery Manufacturing: A Game Changer." International Journal of Advanced Manufacturing Technology.
This blog post provides a comprehensive overview of the manufacturing processes for the latest smart digital product battery cells, highlighting the importance of innovation and sustainability in the industry.
What are the Manufacturing Processes for the Latest Smart Digital Product Battery Cells?
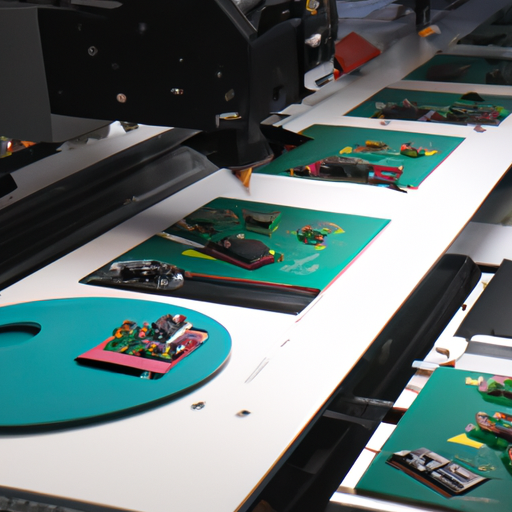
I. Introduction
In an era where smart digital products dominate our daily lives, the importance of advanced battery technology cannot be overstated. From smartphones and laptops to wearables and electric vehicles, these devices rely heavily on efficient, reliable, and long-lasting battery cells. The performance, longevity, and overall user experience of these products are significantly influenced by the quality of their battery cells. This article aims to explore the intricate manufacturing processes behind the latest battery cells used in smart digital products, shedding light on the technologies that power our modern world.
II. Types of Battery Cells Used in Smart Digital Products
A. Lithium-ion (Li-ion) Batteries
Lithium-ion batteries are the most prevalent type of battery used in smart digital products today. Known for their high energy density, lightweight design, and ability to recharge quickly, Li-ion batteries have become the gold standard for portable electronics. They are commonly found in smartphones, laptops, tablets, and electric vehicles, providing the necessary power to keep these devices running efficiently.
B. Solid-state Batteries
Emerging as a promising alternative, solid-state batteries utilize a solid electrolyte instead of a liquid one. This technology offers several advantages, including higher energy density, improved safety, and longer lifespan. While still in the developmental stage, solid-state batteries hold the potential to revolutionize the battery industry, particularly in applications requiring high performance and safety, such as electric vehicles and advanced consumer electronics.
C. Other Battery Technologies
In addition to Li-ion and solid-state batteries, other technologies like lithium polymer (LiPo) and nickel-metal hydride (NiMH) batteries are also used in specific applications. LiPo batteries are favored in devices where weight and form factor are critical, such as drones and wearables. NiMH batteries, while less common in modern smart devices, are still used in some applications due to their reliability and cost-effectiveness.
III. Overview of Battery Cell Manufacturing
The manufacturing of battery cells is a complex process that demands precision and stringent quality control. Each stage of production is crucial to ensure that the final product meets the required performance and safety standards. The key stages in the manufacturing process include material selection, cell design and engineering, and assembly and integration.
IV. Detailed Manufacturing Processes
A. Material Preparation
The first step in battery cell manufacturing is sourcing raw materials, which typically include lithium, cobalt, nickel, and graphite. These materials must undergo purification and processing to remove impurities that could affect battery performance. The quality of the raw materials directly impacts the efficiency and safety of the final battery cells.
B. Electrode Production
Electrode production is a critical phase in battery manufacturing. It involves several steps:
1. **Coating Processes**: A slurry containing active materials, solvents, and binders is coated onto a current collector (usually aluminum for the positive electrode and copper for the negative electrode). This process is crucial for ensuring uniformity and adherence of the active materials.
2. **Drying and Calendaring**: After coating, the electrodes are dried to remove solvents and then passed through rollers (calendaring) to achieve the desired thickness and density.
3. **Cutting and Stacking**: The dried electrodes are cut into specific shapes and sizes, then stacked with separators to form the cell structure.
C. Electrolyte Preparation
The electrolyte is a vital component of battery cells, facilitating the movement of ions between the electrodes. The composition and formulation of electrolytes are carefully designed to optimize performance and safety. Quality checks are performed to ensure that the electrolyte meets the required specifications, including viscosity and conductivity.
D. Cell Assembly
The assembly process involves several steps:
1. **Layering Electrodes and Separators**: The prepared electrodes and separators are layered together in a specific configuration to form the cell.
2. **Filling with Electrolyte**: The assembled cell is filled with the prepared electrolyte, ensuring that all components are adequately saturated.
3. **Sealing and Packaging**: Finally, the cell is sealed to prevent leakage and packaged for distribution. This step is crucial for maintaining the integrity and safety of the battery.
E. Formation and Testing
Once assembled, the battery cells undergo a formation process, which involves initial charging and cycling to activate the materials. This step is essential for ensuring that the battery cells perform as expected. Following formation, rigorous performance testing and quality assurance checks are conducted, including safety testing for thermal, mechanical, and electrical stability.
V. Innovations in Battery Manufacturing
The battery manufacturing landscape is continuously evolving, driven by technological advancements and the need for more efficient production methods. Some notable innovations include:
A. Automation and Robotics
The integration of automation and robotics in battery production has significantly improved efficiency and precision. Automated systems can handle repetitive tasks, reducing the risk of human error and increasing production speed.
B. Advanced Materials and Nanotechnology
Research into advanced materials and nanotechnology is paving the way for the development of next-generation batteries. These innovations aim to enhance energy density, reduce charging times, and improve overall battery performance.
C. Sustainable Manufacturing Practices
As environmental concerns grow, the battery industry is increasingly focusing on sustainable manufacturing practices. This includes recycling and reusing materials, as well as implementing processes that reduce the carbon footprint of production. Companies are exploring ways to minimize waste and energy consumption throughout the manufacturing process.
VI. Challenges in Battery Cell Manufacturing
Despite the advancements in battery technology, several challenges persist in the manufacturing sector:
A. Supply Chain Issues and Material Shortages
The demand for battery materials, particularly lithium and cobalt, has surged, leading to supply chain challenges and material shortages. This can impact production timelines and costs.
B. Environmental Concerns and Regulations
The environmental impact of battery production and disposal is a growing concern. Manufacturers must navigate regulations and implement practices that minimize harm to the environment.
C. Balancing Performance with Cost-Effectiveness
As battery technology advances, manufacturers face the challenge of balancing performance improvements with cost-effectiveness. Developing high-performance batteries that are also affordable for consumers is a critical consideration.
VII. Future Trends in Battery Technology and Manufacturing
The future of battery technology and manufacturing is promising, with several trends on the horizon:
A. Research and Development in Next-Generation Batteries
Ongoing research is focused on developing next-generation batteries, such as lithium-sulfur and lithium-air batteries, which could offer significantly higher energy densities and longer lifespans.
B. The Role of Artificial Intelligence and Machine Learning
Artificial intelligence (AI) and machine learning are increasingly being integrated into battery manufacturing processes. These technologies can optimize production, predict maintenance needs, and enhance quality control.
C. Predictions for the Future of Battery Cells in Smart Digital Products
As smart digital products continue to evolve, the demand for advanced battery cells will only increase. Future trends may include batteries with faster charging capabilities, longer lifespans, and improved safety features, all of which will enhance the user experience.
VIII. Conclusion
The manufacturing processes behind advanced battery cells are complex and multifaceted, playing a crucial role in the performance and longevity of smart digital products. Innovations in battery technology and manufacturing practices are paving the way for a more efficient and sustainable future. As the landscape of battery technology continues to evolve, consumers and manufacturers alike will benefit from the advancements that enhance the functionality and usability of smart devices.
IX. References
1. N. N. (2022). "Advancements in Lithium-Ion Battery Technology." Journal of Power Sources.
2. M. M. (2023). "The Future of Solid-State Batteries." Energy Storage Materials.
3. R. R. (2021). "Sustainable Practices in Battery Manufacturing." Journal of Cleaner Production.
4. T. T. (2023). "AI in Battery Manufacturing: A Game Changer." International Journal of Advanced Manufacturing Technology.
This blog post provides a comprehensive overview of the manufacturing processes for the latest smart digital product battery cells, highlighting the importance of innovation and sustainability in the industry.