Lifting Resistor Product Training Precautions
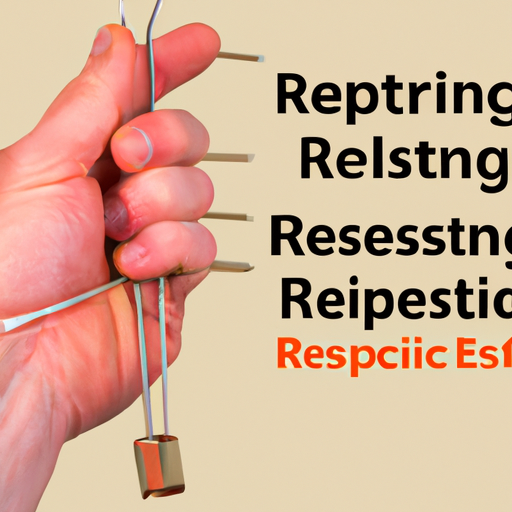
I. Introduction
In the world of electrical engineering, lifting resistors play a crucial role in ensuring the safety and efficiency of various systems. These components are designed to manage electrical loads, dissipate energy, and protect sensitive equipment from damage. However, the proper handling, installation, and maintenance of lifting resistors are paramount to their effectiveness and safety. This blog post aims to provide a comprehensive overview of lifting resistors, the importance of proper training, and essential precautions to consider during their use.
II. Understanding Lifting Resistors
A. What are Lifting Resistors?
Lifting resistors are specialized components used in electrical circuits to manage voltage levels and current flow. Their primary function is to provide a controlled path for electrical energy, ensuring that systems operate within safe parameters. They are commonly used in applications such as power distribution, motor control, and testing equipment.
1. Function and Purpose
The primary purpose of lifting resistors is to limit the current that flows through a circuit, thereby protecting sensitive components from overload. They also help in dissipating excess energy as heat, which is crucial in preventing damage to electrical systems.
2. Common Applications
Lifting resistors are utilized in various applications, including:
Power Systems: To manage load balancing and prevent voltage spikes.
Motor Control: To ensure smooth operation and prevent damage during startup and shutdown.
Testing Equipment: To simulate load conditions and ensure accurate measurements.
B. Types of Lifting Resistors
Lifting resistors come in several types, each designed for specific applications and requirements.
1. Fixed Resistors
Fixed lifting resistors have a predetermined resistance value and are commonly used in applications where consistent performance is required. They are simple to install and maintain, making them a popular choice for many electrical systems.
2. Variable Resistors
Variable lifting resistors allow for adjustable resistance levels, providing flexibility in applications where load conditions may change. These resistors are often used in testing environments and in systems that require fine-tuning of electrical parameters.
3. Specialty Resistors
Specialty lifting resistors are designed for unique applications, such as high-power or high-voltage environments. These resistors may incorporate advanced materials and designs to withstand extreme conditions.
III. Safety Precautions
A. General Safety Guidelines
Safety is paramount when working with lifting resistors. Adhering to general safety guidelines can help prevent accidents and ensure a safe working environment.
1. Personal Protective Equipment (PPE)
Always wear appropriate PPE, including gloves, safety glasses, and insulated footwear, when handling lifting resistors. This equipment helps protect against electrical hazards and physical injuries.
2. Electrical Safety Protocols
Follow established electrical safety protocols, such as de-energizing circuits before working on them and using lockout/tagout procedures to prevent accidental re-energization.
B. Handling and Storage
Proper handling and storage of lifting resistors are essential to maintain their integrity and performance.
1. Proper Handling Techniques
When handling lifting resistors, avoid applying excessive force or dropping them, as this can cause damage. Use appropriate tools and techniques to ensure safe handling.
2. Storage Conditions
Store lifting resistors in a clean, dry environment, away from direct sunlight and extreme temperatures. Proper storage helps prevent degradation and ensures the longevity of the components.
C. Risk Assessment
Conducting a thorough risk assessment is crucial to identify potential hazards associated with lifting resistors.
1. Identifying Potential Hazards
Evaluate the work environment and identify potential hazards, such as electrical shock, overheating, or mechanical failure.
2. Mitigation Strategies
Implement mitigation strategies to address identified risks, such as providing adequate training, using appropriate PPE, and ensuring proper installation procedures are followed.
IV. Training Requirements
A. Target Audience for Training
Training is essential for anyone involved in the handling, installation, or maintenance of lifting resistors.
1. Engineers and Technicians
Engineers and technicians must have a solid understanding of lifting resistors, their applications, and safety protocols to ensure effective and safe use.
2. Safety Personnel
Safety personnel play a critical role in enforcing safety standards and ensuring that all team members are trained in proper procedures.
B. Key Training Components
Effective training should encompass several key components.
1. Theoretical Knowledge
Participants should gain a thorough understanding of lifting resistors, including their function, types, and applications.
2. Practical Skills
Hands-on training is essential to develop practical skills in handling, installing, and maintaining lifting resistors.
3. Emergency Procedures
Training should also cover emergency procedures, including how to respond to electrical accidents or equipment failures.
V. Installation Precautions
A. Site Preparation
Proper site preparation is crucial for the successful installation of lifting resistors.
1. Environmental Considerations
Evaluate the installation environment for factors such as temperature, humidity, and potential contaminants that could affect the performance of lifting resistors.
2. Equipment Readiness
Ensure that all necessary tools and equipment are available and in good working condition before beginning the installation process.
B. Installation Procedures
Following a systematic installation procedure can help prevent mistakes and ensure the safe operation of lifting resistors.
1. Step-by-Step Installation Guide
1. **Review Specifications**: Understand the specifications and requirements for the lifting resistor being installed.
2. **Prepare the Site**: Ensure the installation area is clean and free of hazards.
3. **Install the Resistor**: Follow the manufacturer's guidelines for installation, ensuring all connections are secure.
4. **Test the Installation**: Conduct tests to verify that the installation is functioning correctly.
2. Common Mistakes to Avoid
Avoid common mistakes such as improper connections, neglecting to follow safety protocols, and failing to conduct thorough testing after installation.
VI. Operational Precautions
A. Monitoring and Maintenance
Regular monitoring and maintenance are essential to ensure the continued performance and safety of lifting resistors.
1. Regular Inspection Protocols
Establish a schedule for regular inspections to identify any signs of wear, damage, or malfunction.
2. Maintenance Best Practices
Follow best practices for maintenance, including cleaning, tightening connections, and replacing worn components as needed.
B. Troubleshooting Common Issues
Being able to troubleshoot common issues can help prevent prolonged downtime and ensure the safe operation of lifting resistors.
1. Identifying Symptoms of Failure
Common symptoms of failure may include overheating, unusual noises, or erratic performance. Recognizing these signs early can help prevent further damage.
2. Corrective Actions
Implement corrective actions promptly, such as replacing faulty components or adjusting settings to restore proper function.
VII. Compliance and Standards
A. Industry Standards and Regulations
Adhering to industry standards and regulations is essential for ensuring the safety and reliability of lifting resistors.
1. Relevant Codes and Guidelines
Familiarize yourself with relevant codes and guidelines that govern the use of lifting resistors in your industry.
2. Importance of Compliance
Compliance with industry standards helps ensure the safety of personnel and equipment, as well as the overall integrity of electrical systems.
B. Documentation and Record-Keeping
Maintaining accurate documentation and records is crucial for compliance and safety.
1. Training Records
Keep detailed records of all training sessions, including participant names, dates, and topics covered.
2. Maintenance Logs
Maintain logs of all maintenance activities, inspections, and repairs performed on lifting resistors to ensure accountability and traceability.
VIII. Conclusion
In conclusion, lifting resistors are vital components in electrical systems, and their proper handling, installation, and maintenance are essential for safety and performance. By understanding the importance of training, adhering to safety precautions, and following best practices, engineers, technicians, and safety personnel can ensure the effective use of lifting resistors. Ongoing education and continuous improvement in safety practices are crucial for fostering a culture of safety and reliability in the workplace.
IX. References
For further reading and resources on lifting resistors and safety practices, consider the following:
- Suggested reading materials on electrical safety and component handling.
- Relevant industry resources, including guidelines from organizations such as the National Electrical Manufacturers Association (NEMA) and the Institute of Electrical and Electronics Engineers (IEEE).
- Contact information for further training opportunities and workshops on lifting resistors and electrical safety.
By prioritizing safety and education, we can ensure that lifting resistors are used effectively and responsibly in all applications.
Lifting Resistor Product Training Precautions
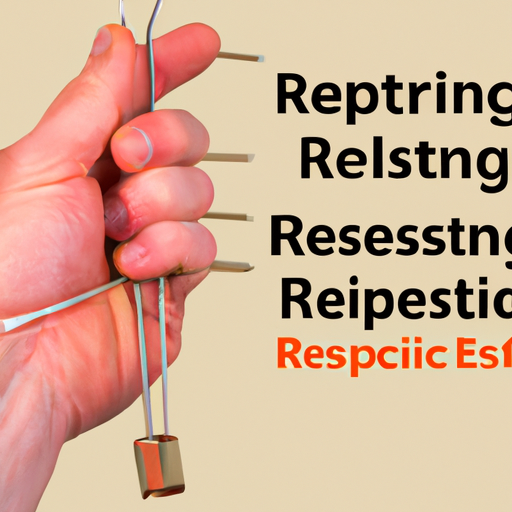
I. Introduction
In the world of electrical engineering, lifting resistors play a crucial role in ensuring the safety and efficiency of various systems. These components are designed to manage electrical loads, dissipate energy, and protect sensitive equipment from damage. However, the proper handling, installation, and maintenance of lifting resistors are paramount to their effectiveness and safety. This blog post aims to provide a comprehensive overview of lifting resistors, the importance of proper training, and essential precautions to consider during their use.
II. Understanding Lifting Resistors
A. What are Lifting Resistors?
Lifting resistors are specialized components used in electrical circuits to manage voltage levels and current flow. Their primary function is to provide a controlled path for electrical energy, ensuring that systems operate within safe parameters. They are commonly used in applications such as power distribution, motor control, and testing equipment.
1. Function and Purpose
The primary purpose of lifting resistors is to limit the current that flows through a circuit, thereby protecting sensitive components from overload. They also help in dissipating excess energy as heat, which is crucial in preventing damage to electrical systems.
2. Common Applications
Lifting resistors are utilized in various applications, including:
Power Systems: To manage load balancing and prevent voltage spikes.
Motor Control: To ensure smooth operation and prevent damage during startup and shutdown.
Testing Equipment: To simulate load conditions and ensure accurate measurements.
B. Types of Lifting Resistors
Lifting resistors come in several types, each designed for specific applications and requirements.
1. Fixed Resistors
Fixed lifting resistors have a predetermined resistance value and are commonly used in applications where consistent performance is required. They are simple to install and maintain, making them a popular choice for many electrical systems.
2. Variable Resistors
Variable lifting resistors allow for adjustable resistance levels, providing flexibility in applications where load conditions may change. These resistors are often used in testing environments and in systems that require fine-tuning of electrical parameters.
3. Specialty Resistors
Specialty lifting resistors are designed for unique applications, such as high-power or high-voltage environments. These resistors may incorporate advanced materials and designs to withstand extreme conditions.
III. Safety Precautions
A. General Safety Guidelines
Safety is paramount when working with lifting resistors. Adhering to general safety guidelines can help prevent accidents and ensure a safe working environment.
1. Personal Protective Equipment (PPE)
Always wear appropriate PPE, including gloves, safety glasses, and insulated footwear, when handling lifting resistors. This equipment helps protect against electrical hazards and physical injuries.
2. Electrical Safety Protocols
Follow established electrical safety protocols, such as de-energizing circuits before working on them and using lockout/tagout procedures to prevent accidental re-energization.
B. Handling and Storage
Proper handling and storage of lifting resistors are essential to maintain their integrity and performance.
1. Proper Handling Techniques
When handling lifting resistors, avoid applying excessive force or dropping them, as this can cause damage. Use appropriate tools and techniques to ensure safe handling.
2. Storage Conditions
Store lifting resistors in a clean, dry environment, away from direct sunlight and extreme temperatures. Proper storage helps prevent degradation and ensures the longevity of the components.
C. Risk Assessment
Conducting a thorough risk assessment is crucial to identify potential hazards associated with lifting resistors.
1. Identifying Potential Hazards
Evaluate the work environment and identify potential hazards, such as electrical shock, overheating, or mechanical failure.
2. Mitigation Strategies
Implement mitigation strategies to address identified risks, such as providing adequate training, using appropriate PPE, and ensuring proper installation procedures are followed.
IV. Training Requirements
A. Target Audience for Training
Training is essential for anyone involved in the handling, installation, or maintenance of lifting resistors.
1. Engineers and Technicians
Engineers and technicians must have a solid understanding of lifting resistors, their applications, and safety protocols to ensure effective and safe use.
2. Safety Personnel
Safety personnel play a critical role in enforcing safety standards and ensuring that all team members are trained in proper procedures.
B. Key Training Components
Effective training should encompass several key components.
1. Theoretical Knowledge
Participants should gain a thorough understanding of lifting resistors, including their function, types, and applications.
2. Practical Skills
Hands-on training is essential to develop practical skills in handling, installing, and maintaining lifting resistors.
3. Emergency Procedures
Training should also cover emergency procedures, including how to respond to electrical accidents or equipment failures.
V. Installation Precautions
A. Site Preparation
Proper site preparation is crucial for the successful installation of lifting resistors.
1. Environmental Considerations
Evaluate the installation environment for factors such as temperature, humidity, and potential contaminants that could affect the performance of lifting resistors.
2. Equipment Readiness
Ensure that all necessary tools and equipment are available and in good working condition before beginning the installation process.
B. Installation Procedures
Following a systematic installation procedure can help prevent mistakes and ensure the safe operation of lifting resistors.
1. Step-by-Step Installation Guide
1. **Review Specifications**: Understand the specifications and requirements for the lifting resistor being installed.
2. **Prepare the Site**: Ensure the installation area is clean and free of hazards.
3. **Install the Resistor**: Follow the manufacturer's guidelines for installation, ensuring all connections are secure.
4. **Test the Installation**: Conduct tests to verify that the installation is functioning correctly.
2. Common Mistakes to Avoid
Avoid common mistakes such as improper connections, neglecting to follow safety protocols, and failing to conduct thorough testing after installation.
VI. Operational Precautions
A. Monitoring and Maintenance
Regular monitoring and maintenance are essential to ensure the continued performance and safety of lifting resistors.
1. Regular Inspection Protocols
Establish a schedule for regular inspections to identify any signs of wear, damage, or malfunction.
2. Maintenance Best Practices
Follow best practices for maintenance, including cleaning, tightening connections, and replacing worn components as needed.
B. Troubleshooting Common Issues
Being able to troubleshoot common issues can help prevent prolonged downtime and ensure the safe operation of lifting resistors.
1. Identifying Symptoms of Failure
Common symptoms of failure may include overheating, unusual noises, or erratic performance. Recognizing these signs early can help prevent further damage.
2. Corrective Actions
Implement corrective actions promptly, such as replacing faulty components or adjusting settings to restore proper function.
VII. Compliance and Standards
A. Industry Standards and Regulations
Adhering to industry standards and regulations is essential for ensuring the safety and reliability of lifting resistors.
1. Relevant Codes and Guidelines
Familiarize yourself with relevant codes and guidelines that govern the use of lifting resistors in your industry.
2. Importance of Compliance
Compliance with industry standards helps ensure the safety of personnel and equipment, as well as the overall integrity of electrical systems.
B. Documentation and Record-Keeping
Maintaining accurate documentation and records is crucial for compliance and safety.
1. Training Records
Keep detailed records of all training sessions, including participant names, dates, and topics covered.
2. Maintenance Logs
Maintain logs of all maintenance activities, inspections, and repairs performed on lifting resistors to ensure accountability and traceability.
VIII. Conclusion
In conclusion, lifting resistors are vital components in electrical systems, and their proper handling, installation, and maintenance are essential for safety and performance. By understanding the importance of training, adhering to safety precautions, and following best practices, engineers, technicians, and safety personnel can ensure the effective use of lifting resistors. Ongoing education and continuous improvement in safety practices are crucial for fostering a culture of safety and reliability in the workplace.
IX. References
For further reading and resources on lifting resistors and safety practices, consider the following:
- Suggested reading materials on electrical safety and component handling.
- Relevant industry resources, including guidelines from organizations such as the National Electrical Manufacturers Association (NEMA) and the Institute of Electrical and Electronics Engineers (IEEE).
- Contact information for further training opportunities and workshops on lifting resistors and electrical safety.
By prioritizing safety and education, we can ensure that lifting resistors are used effectively and responsibly in all applications.