What are the Product Standards for Resistor Classification?
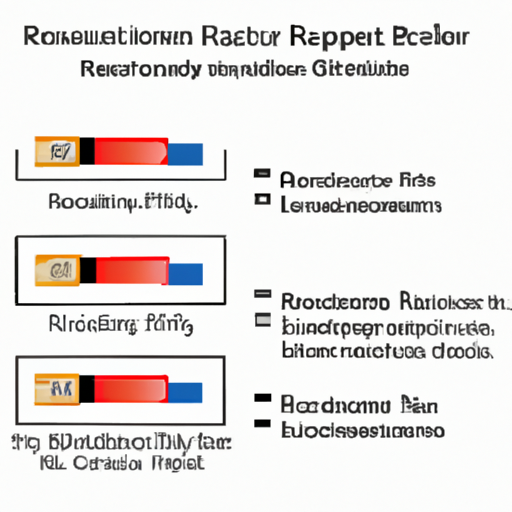
I. Introduction
A. Definition of Resistors
Resistors are passive electronic components that limit the flow of electric current in a circuit. They are essential in controlling voltage and current levels, ensuring that electronic devices operate safely and effectively. Resistors come in various forms and materials, each designed for specific applications and performance requirements.
B. Importance of Resistor Classification
The classification of resistors is crucial for several reasons. It helps manufacturers and engineers select the appropriate resistor for a given application, ensuring optimal performance and reliability. Proper classification also aids in standardizing production processes, which is vital for quality assurance and compliance with regulatory requirements. Furthermore, understanding resistor types and their specifications can significantly impact the design and functionality of electronic circuits.
C. Overview of Product Standards
Product standards for resistors provide guidelines and specifications that manufacturers must adhere to during production. These standards ensure that resistors meet specific performance criteria, safety requirements, and environmental regulations. By following these standards, manufacturers can produce reliable and consistent products that meet the needs of various industries.
II. Types of Resistors
A. Fixed Resistors
Fixed resistors have a constant resistance value and are the most common type used in electronic circuits. They can be further classified into several categories:
1. **Carbon Composition Resistors**: Made from a mixture of carbon and a binding material, these resistors are known for their high energy absorption and ability to withstand high temperatures. However, they have a relatively high tolerance and are less stable over time.
2. **Metal Film Resistors**: These resistors are made by depositing a thin layer of metal onto a ceramic substrate. They offer better stability, lower noise, and tighter tolerances compared to carbon composition resistors, making them suitable for precision applications.
3. **Wirewound Resistors**: Constructed by winding a metal wire around a ceramic or fiberglass core, wirewound resistors can handle high power levels and are often used in applications requiring high precision and stability.
B. Variable Resistors
Variable resistors allow for adjustable resistance values, making them versatile components in electronic circuits. They include:
1. **Potentiometers**: These are commonly used for adjusting voltage levels in circuits, such as volume controls in audio equipment. They consist of a resistive element and a movable wiper that changes the resistance.
2. **Rheostats**: Similar to potentiometers, rheostats are used to control current flow in a circuit. They typically have higher power ratings and are used in applications like dimmer switches and motor speed controls.
C. Specialty Resistors
Specialty resistors are designed for specific applications and include:
1. **Thermistors**: These temperature-sensitive resistors change resistance with temperature variations. They are widely used in temperature sensing and control applications.
2. **Photoresistors**: Also known as light-dependent resistors (LDRs), these components change resistance based on light exposure. They are commonly used in light-sensing applications, such as automatic lighting systems.
III. Key Product Standards for Resistors
A. International Electrotechnical Commission (IEC) Standards
The IEC sets international standards for electrical and electronic devices, including resistors. Key standards include:
1. **IEC 60115 - Fixed Resistors**: This standard outlines the performance requirements, testing methods, and classification of fixed resistors, ensuring consistency and reliability across products.
2. **IEC 60384 - Fixed Capacitors and Resistors**: This standard provides guidelines for the performance and safety of fixed capacitors and resistors, promoting compatibility and interoperability in electronic devices.
B. American National Standards Institute (ANSI) Standards
The ANSI develops standards for various industries, including electronics. The ANSI/IEEE standards provide guidelines for resistor performance, testing, and safety, ensuring that products meet the necessary quality and reliability criteria.
C. Underwriters Laboratories (UL) Standards
UL is a global safety certification organization that establishes safety standards for electrical devices.
1. **UL 1412 - Resistors**: This standard focuses on the safety and performance of resistors, ensuring that they can operate safely under specified conditions.
D. Other Relevant Standards
1. **RoHS Compliance**: The Restriction of Hazardous Substances (RoHS) directive limits the use of specific hazardous materials in electrical and electronic equipment, promoting environmental sustainability.
2. **REACH Regulations**: The Registration, Evaluation, Authorisation, and Restriction of Chemicals (REACH) regulations ensure that chemical substances used in products are safe for human health and the environment.
IV. Classification Criteria for Resistors
A. Resistance Value
1. **Ohmic Value Range**: Resistors are classified based on their resistance values, which can range from fractions of an ohm to several megaohms, depending on the application.
2. **Tolerance Levels**: Tolerance indicates the allowable deviation from the specified resistance value. Common tolerance levels include ±1%, ±5%, and ±10%, with tighter tolerances used in precision applications.
B. Power Rating
1. **Wattage Ratings**: Resistors are rated for the maximum power they can dissipate without overheating. Common ratings include 1/8W, 1/4W, 1W, and higher for specialized applications.
2. **Thermal Considerations**: The thermal performance of resistors is critical, as excessive heat can lead to failure. Manufacturers must consider heat dissipation and cooling methods in their designs.
C. Temperature Coefficient
1. **Temperature Stability**: The temperature coefficient indicates how much a resistor's value changes with temperature. Low-temperature coefficients are preferred for precision applications.
2. **Impact on Performance**: Variations in temperature can affect resistor performance, making it essential to select resistors with appropriate temperature coefficients for specific applications.
D. Voltage Rating
1. **Maximum Operating Voltage**: Resistors have a maximum voltage rating, beyond which they may fail or become damaged. This rating is crucial for ensuring safe operation in circuits.
2. **Breakdown Voltage**: The breakdown voltage is the point at which a resistor can no longer withstand the applied voltage, leading to potential failure. Understanding this parameter is vital for circuit design.
V. Testing and Quality Assurance
A. Testing Methods
1. **Resistance Measurement**: Accurate measurement of resistance values is essential for quality control. Various methods, including four-wire measurements, are used to ensure precision.
2. **Power Rating Tests**: Resistors undergo power rating tests to verify their ability to handle specified wattage without overheating or failing.
3. **Environmental Testing**: Resistors are subjected to environmental tests, including humidity, temperature cycling, and vibration, to ensure reliability under various conditions.
B. Quality Assurance Protocols
1. **ISO 9001 Certification**: Many manufacturers seek ISO 9001 certification to demonstrate their commitment to quality management systems and continuous improvement.
2. **Continuous Monitoring and Improvement**: Ongoing monitoring of production processes and product performance is essential for maintaining quality and meeting industry standards.
VI. Applications of Resistor Standards
A. Consumer Electronics
Resistor standards play a vital role in consumer electronics, ensuring that devices such as smartphones, televisions, and audio equipment operate reliably and safely.
B. Automotive Industry
In the automotive sector, resistors are used in various applications, including engine control units, safety systems, and infotainment systems. Adhering to standards ensures the safety and performance of these critical components.
C. Industrial Equipment
Industrial equipment relies on resistors for control and monitoring functions. Standards help ensure that these components can withstand harsh operating conditions and deliver consistent performance.
D. Medical Devices
In medical devices, precision and reliability are paramount. Resistor standards ensure that components meet stringent safety and performance requirements, contributing to the overall effectiveness of medical technology.
VII. Challenges and Future Trends
A. Evolving Technology and Standards
As technology advances, resistor standards must evolve to address new materials, manufacturing processes, and applications. Staying current with these changes is essential for manufacturers and engineers.
B. Environmental Considerations
Increasing awareness of environmental issues is driving the development of more sustainable resistor materials and manufacturing processes. Compliance with regulations like RoHS and REACH is becoming increasingly important.
C. The Role of Smart Resistors
The emergence of smart resistors, which can adapt their resistance based on environmental conditions or user input, presents new opportunities and challenges for resistor classification and standards.
VIII. Conclusion
A. Summary of Key Points
Resistor classification is essential for ensuring the proper functioning of electronic devices. Understanding the various types of resistors, key product standards, and classification criteria is crucial for manufacturers and engineers alike.
B. Importance of Adhering to Standards
Adhering to established standards not only ensures product quality and safety but also fosters innovation and competitiveness in the electronics industry.
C. Future Outlook for Resistor Classification Standards
As technology continues to evolve, the future of resistor classification standards will likely focus on sustainability, adaptability, and enhanced performance, paving the way for new applications and advancements in electronic design.
IX. References
A. List of Standards Organizations
- International Electrotechnical Commission (IEC)
- American National Standards Institute (ANSI)
- Underwriters Laboratories (UL)
B. Relevant Literature and Resources
- IEC Standards Documentation
- ANSI/IEEE Standards Publications
- UL Certification Guidelines
C. Industry Publications and Journals
- Journal of Electronic Materials
- IEEE Transactions on Components, Packaging and Manufacturing Technology
- Electronics Weekly
This comprehensive overview of product standards for resistor classification highlights the importance of these components in modern electronics and the need for adherence to established guidelines to ensure safety, reliability, and performance.
What are the Product Standards for Resistor Classification?
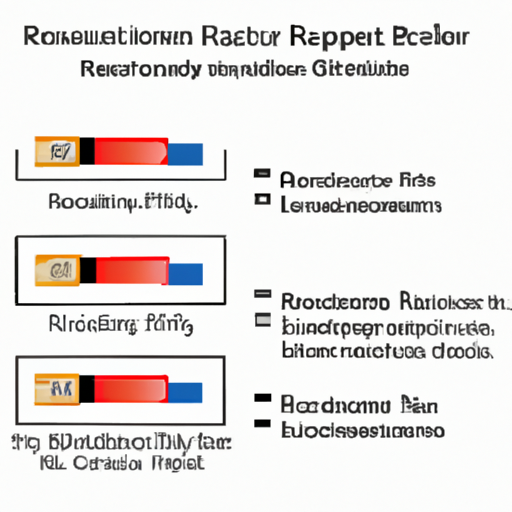
I. Introduction
A. Definition of Resistors
Resistors are passive electronic components that limit the flow of electric current in a circuit. They are essential in controlling voltage and current levels, ensuring that electronic devices operate safely and effectively. Resistors come in various forms and materials, each designed for specific applications and performance requirements.
B. Importance of Resistor Classification
The classification of resistors is crucial for several reasons. It helps manufacturers and engineers select the appropriate resistor for a given application, ensuring optimal performance and reliability. Proper classification also aids in standardizing production processes, which is vital for quality assurance and compliance with regulatory requirements. Furthermore, understanding resistor types and their specifications can significantly impact the design and functionality of electronic circuits.
C. Overview of Product Standards
Product standards for resistors provide guidelines and specifications that manufacturers must adhere to during production. These standards ensure that resistors meet specific performance criteria, safety requirements, and environmental regulations. By following these standards, manufacturers can produce reliable and consistent products that meet the needs of various industries.
II. Types of Resistors
A. Fixed Resistors
Fixed resistors have a constant resistance value and are the most common type used in electronic circuits. They can be further classified into several categories:
1. **Carbon Composition Resistors**: Made from a mixture of carbon and a binding material, these resistors are known for their high energy absorption and ability to withstand high temperatures. However, they have a relatively high tolerance and are less stable over time.
2. **Metal Film Resistors**: These resistors are made by depositing a thin layer of metal onto a ceramic substrate. They offer better stability, lower noise, and tighter tolerances compared to carbon composition resistors, making them suitable for precision applications.
3. **Wirewound Resistors**: Constructed by winding a metal wire around a ceramic or fiberglass core, wirewound resistors can handle high power levels and are often used in applications requiring high precision and stability.
B. Variable Resistors
Variable resistors allow for adjustable resistance values, making them versatile components in electronic circuits. They include:
1. **Potentiometers**: These are commonly used for adjusting voltage levels in circuits, such as volume controls in audio equipment. They consist of a resistive element and a movable wiper that changes the resistance.
2. **Rheostats**: Similar to potentiometers, rheostats are used to control current flow in a circuit. They typically have higher power ratings and are used in applications like dimmer switches and motor speed controls.
C. Specialty Resistors
Specialty resistors are designed for specific applications and include:
1. **Thermistors**: These temperature-sensitive resistors change resistance with temperature variations. They are widely used in temperature sensing and control applications.
2. **Photoresistors**: Also known as light-dependent resistors (LDRs), these components change resistance based on light exposure. They are commonly used in light-sensing applications, such as automatic lighting systems.
III. Key Product Standards for Resistors
A. International Electrotechnical Commission (IEC) Standards
The IEC sets international standards for electrical and electronic devices, including resistors. Key standards include:
1. **IEC 60115 - Fixed Resistors**: This standard outlines the performance requirements, testing methods, and classification of fixed resistors, ensuring consistency and reliability across products.
2. **IEC 60384 - Fixed Capacitors and Resistors**: This standard provides guidelines for the performance and safety of fixed capacitors and resistors, promoting compatibility and interoperability in electronic devices.
B. American National Standards Institute (ANSI) Standards
The ANSI develops standards for various industries, including electronics. The ANSI/IEEE standards provide guidelines for resistor performance, testing, and safety, ensuring that products meet the necessary quality and reliability criteria.
C. Underwriters Laboratories (UL) Standards
UL is a global safety certification organization that establishes safety standards for electrical devices.
1. **UL 1412 - Resistors**: This standard focuses on the safety and performance of resistors, ensuring that they can operate safely under specified conditions.
D. Other Relevant Standards
1. **RoHS Compliance**: The Restriction of Hazardous Substances (RoHS) directive limits the use of specific hazardous materials in electrical and electronic equipment, promoting environmental sustainability.
2. **REACH Regulations**: The Registration, Evaluation, Authorisation, and Restriction of Chemicals (REACH) regulations ensure that chemical substances used in products are safe for human health and the environment.
IV. Classification Criteria for Resistors
A. Resistance Value
1. **Ohmic Value Range**: Resistors are classified based on their resistance values, which can range from fractions of an ohm to several megaohms, depending on the application.
2. **Tolerance Levels**: Tolerance indicates the allowable deviation from the specified resistance value. Common tolerance levels include ±1%, ±5%, and ±10%, with tighter tolerances used in precision applications.
B. Power Rating
1. **Wattage Ratings**: Resistors are rated for the maximum power they can dissipate without overheating. Common ratings include 1/8W, 1/4W, 1W, and higher for specialized applications.
2. **Thermal Considerations**: The thermal performance of resistors is critical, as excessive heat can lead to failure. Manufacturers must consider heat dissipation and cooling methods in their designs.
C. Temperature Coefficient
1. **Temperature Stability**: The temperature coefficient indicates how much a resistor's value changes with temperature. Low-temperature coefficients are preferred for precision applications.
2. **Impact on Performance**: Variations in temperature can affect resistor performance, making it essential to select resistors with appropriate temperature coefficients for specific applications.
D. Voltage Rating
1. **Maximum Operating Voltage**: Resistors have a maximum voltage rating, beyond which they may fail or become damaged. This rating is crucial for ensuring safe operation in circuits.
2. **Breakdown Voltage**: The breakdown voltage is the point at which a resistor can no longer withstand the applied voltage, leading to potential failure. Understanding this parameter is vital for circuit design.
V. Testing and Quality Assurance
A. Testing Methods
1. **Resistance Measurement**: Accurate measurement of resistance values is essential for quality control. Various methods, including four-wire measurements, are used to ensure precision.
2. **Power Rating Tests**: Resistors undergo power rating tests to verify their ability to handle specified wattage without overheating or failing.
3. **Environmental Testing**: Resistors are subjected to environmental tests, including humidity, temperature cycling, and vibration, to ensure reliability under various conditions.
B. Quality Assurance Protocols
1. **ISO 9001 Certification**: Many manufacturers seek ISO 9001 certification to demonstrate their commitment to quality management systems and continuous improvement.
2. **Continuous Monitoring and Improvement**: Ongoing monitoring of production processes and product performance is essential for maintaining quality and meeting industry standards.
VI. Applications of Resistor Standards
A. Consumer Electronics
Resistor standards play a vital role in consumer electronics, ensuring that devices such as smartphones, televisions, and audio equipment operate reliably and safely.
B. Automotive Industry
In the automotive sector, resistors are used in various applications, including engine control units, safety systems, and infotainment systems. Adhering to standards ensures the safety and performance of these critical components.
C. Industrial Equipment
Industrial equipment relies on resistors for control and monitoring functions. Standards help ensure that these components can withstand harsh operating conditions and deliver consistent performance.
D. Medical Devices
In medical devices, precision and reliability are paramount. Resistor standards ensure that components meet stringent safety and performance requirements, contributing to the overall effectiveness of medical technology.
VII. Challenges and Future Trends
A. Evolving Technology and Standards
As technology advances, resistor standards must evolve to address new materials, manufacturing processes, and applications. Staying current with these changes is essential for manufacturers and engineers.
B. Environmental Considerations
Increasing awareness of environmental issues is driving the development of more sustainable resistor materials and manufacturing processes. Compliance with regulations like RoHS and REACH is becoming increasingly important.
C. The Role of Smart Resistors
The emergence of smart resistors, which can adapt their resistance based on environmental conditions or user input, presents new opportunities and challenges for resistor classification and standards.
VIII. Conclusion
A. Summary of Key Points
Resistor classification is essential for ensuring the proper functioning of electronic devices. Understanding the various types of resistors, key product standards, and classification criteria is crucial for manufacturers and engineers alike.
B. Importance of Adhering to Standards
Adhering to established standards not only ensures product quality and safety but also fosters innovation and competitiveness in the electronics industry.
C. Future Outlook for Resistor Classification Standards
As technology continues to evolve, the future of resistor classification standards will likely focus on sustainability, adaptability, and enhanced performance, paving the way for new applications and advancements in electronic design.
IX. References
A. List of Standards Organizations
- International Electrotechnical Commission (IEC)
- American National Standards Institute (ANSI)
- Underwriters Laboratories (UL)
B. Relevant Literature and Resources
- IEC Standards Documentation
- ANSI/IEEE Standards Publications
- UL Certification Guidelines
C. Industry Publications and Journals
- Journal of Electronic Materials
- IEEE Transactions on Components, Packaging and Manufacturing Technology
- Electronics Weekly
This comprehensive overview of product standards for resistor classification highlights the importance of these components in modern electronics and the need for adherence to established guidelines to ensure safety, reliability, and performance.